Nuclear business
Currently the company focuses its nuclear business on the first part of the fuel cycle that it markets both nationally and internationally.
Our business areas
Uranium Supply
Design and Engineering
Manufacturing
Services at the Plant
Dismantling and Radioactive Waste Management
Uranium Supply
We maintain a policy of diversification of flexibility sources, supply security, and demanding pricing.
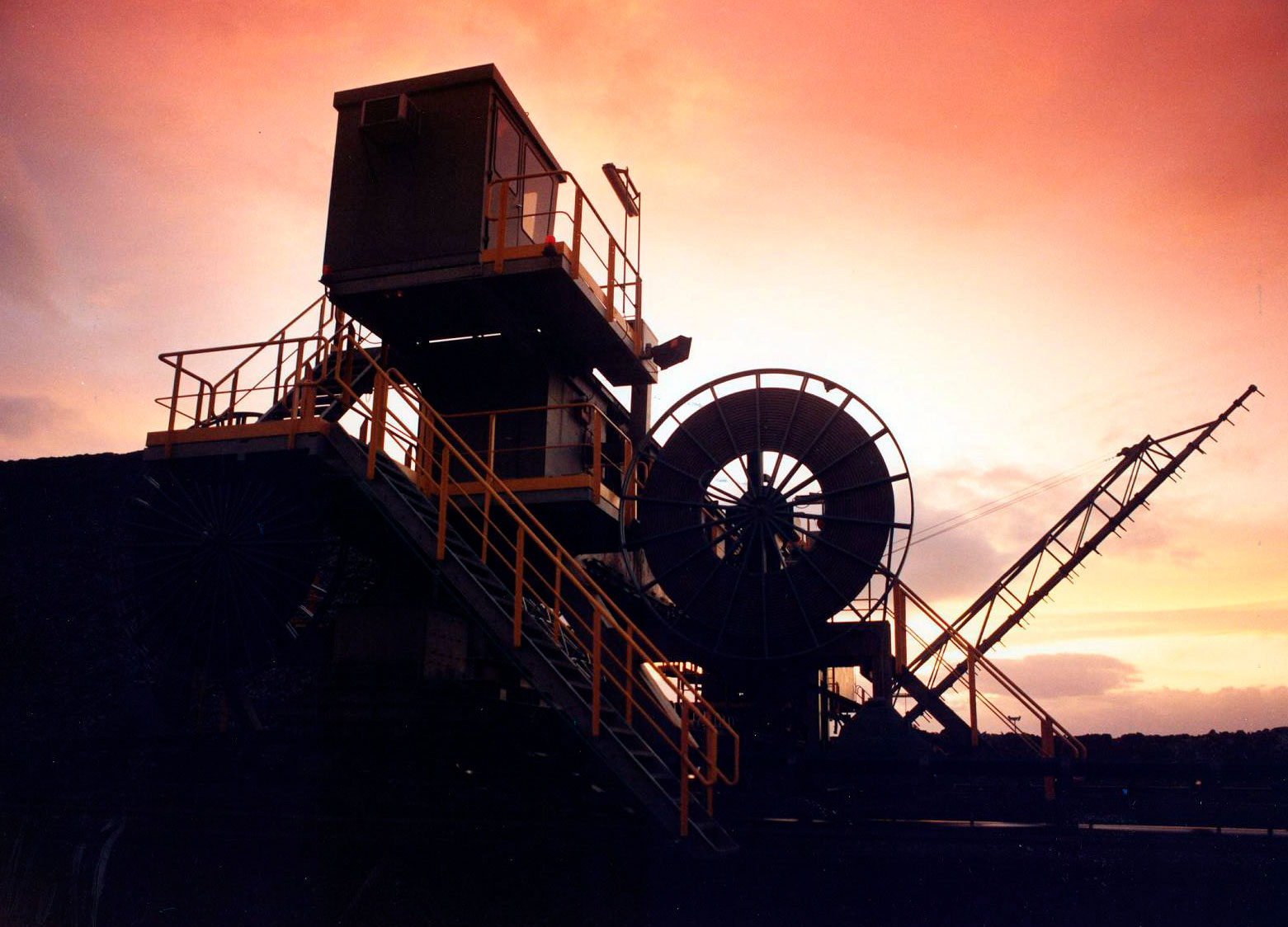
In ENUSA, we manage the enriched uranium supply to the electric companies that own the Spanish nuclear power plants.
We carry out the procurement of supplies with major global suppliers and maintain contracts with main global suppliers of uranium concentrates, conversion services, and enrichment services.
Our portfolio of suppliers allows us to maintain a policy of diversification of sources of flexibility, security of supply and very demanding prices.
In addition to the purchase, we carry out the logistics management de los movimientos de uranio que se tienen que producir hasta la obtención del producto final: el uranio enriquecido.
Enusa guarantees supply to its customers, managing uranium stocks in several countries in order to provide service and security in this phase of the nuclear fuel cycle.
Design and Engineering
Our fuel engineering covers everything from conceptual development and introduction to storage and transport.

We have the latest technological advances through transfer agreements with our partners and licensors Westinghouse and General Electric (GE).This allows us to cover the design, manufacture and supply of fuel to domestic and foreign nuclear power plants, as well as all engineering services related to the management and optimisation of fuel use in the reactor.
The fuel engineering developed at ENUSA covers all technical aspects of the nuclear fuel lifetime: from conceptual development and introduction of new products for irradiation in commercial PWR and BWR reactors, to storage and transport in dry casks as irradiated fuel.
These stages in the life of the fuel go through the following phases:
01
The development and introduction of new products and design methodologies
02
The engineering of reloads and their safety analysis
03
The definition of the product to be manufactured and manufacturing support
04
Monitoring fuel behaviour in the core
05
Analysis of operational experience and subsequent feedback of the design and its tools.
06
Characterisation and analysis for the classification of irradiated fuel for dry storage and transport.
We have more than 30 years of experience in fuel design and licensing in several European countries.
Thanks to our experience, we cover nuclear design aspects and radiological, mechanical, thermo-mechanical, thermo-hydraulic calculations of materials.
These activities are made possible because of the high qualification of ENUSA personnel and the use of calculation tools developed in-house and/or by our licensors Westinghouse and GE.
This knowledge and experience of fuel, its design and behaviour, as well as the integrated view of the whole life of nuclear fuel allow us to provide our customers with a unique set of high added-value services. They also allow us, either autonomously or in collaboration with technology partners, to develop new nuclear fuel fabrication and inspection equipment.
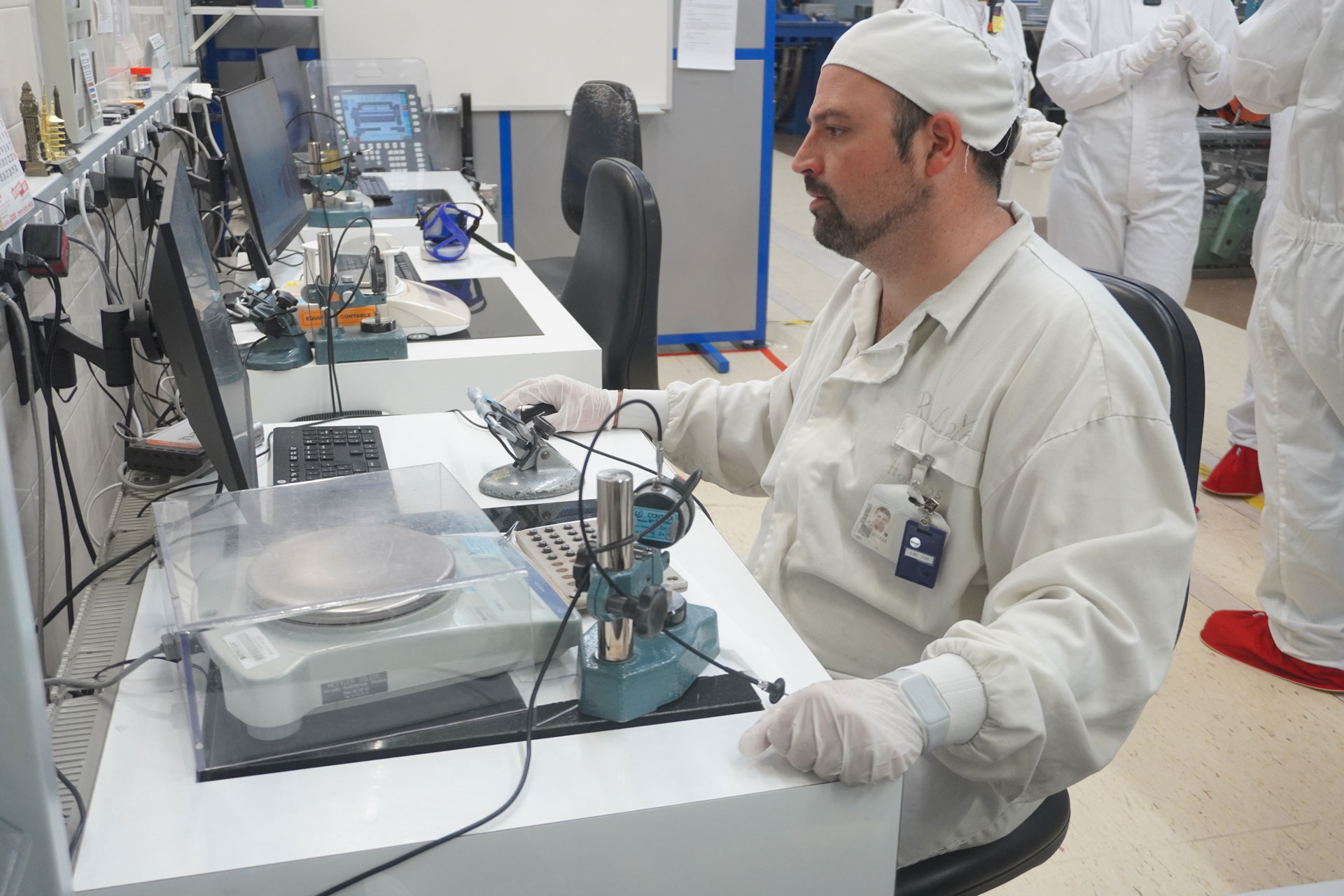
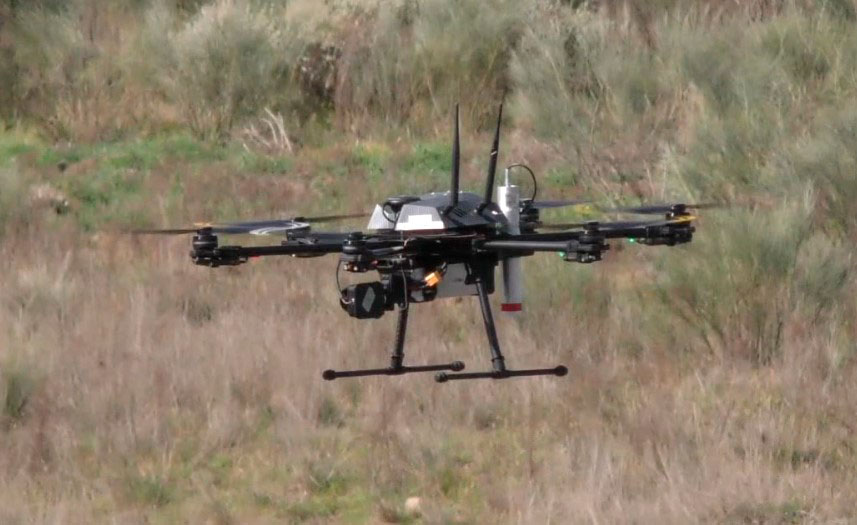
Programa de I+D+I
In ENUSA, engineering is supported by powerful R&D&I, cooperating with Spanish universities through collaboration projects or participation in training activities, and in the promotion of and/or participation in national and international projects on key technical aspects of fuel.
Our fuel engineering has nearly thirty years of experience in fuel design and licensing in several European countries.
Manufacturing
We manufacture for Spanish and European nuclear power plants, integrating the most innovative technology and the latest advances on the market.
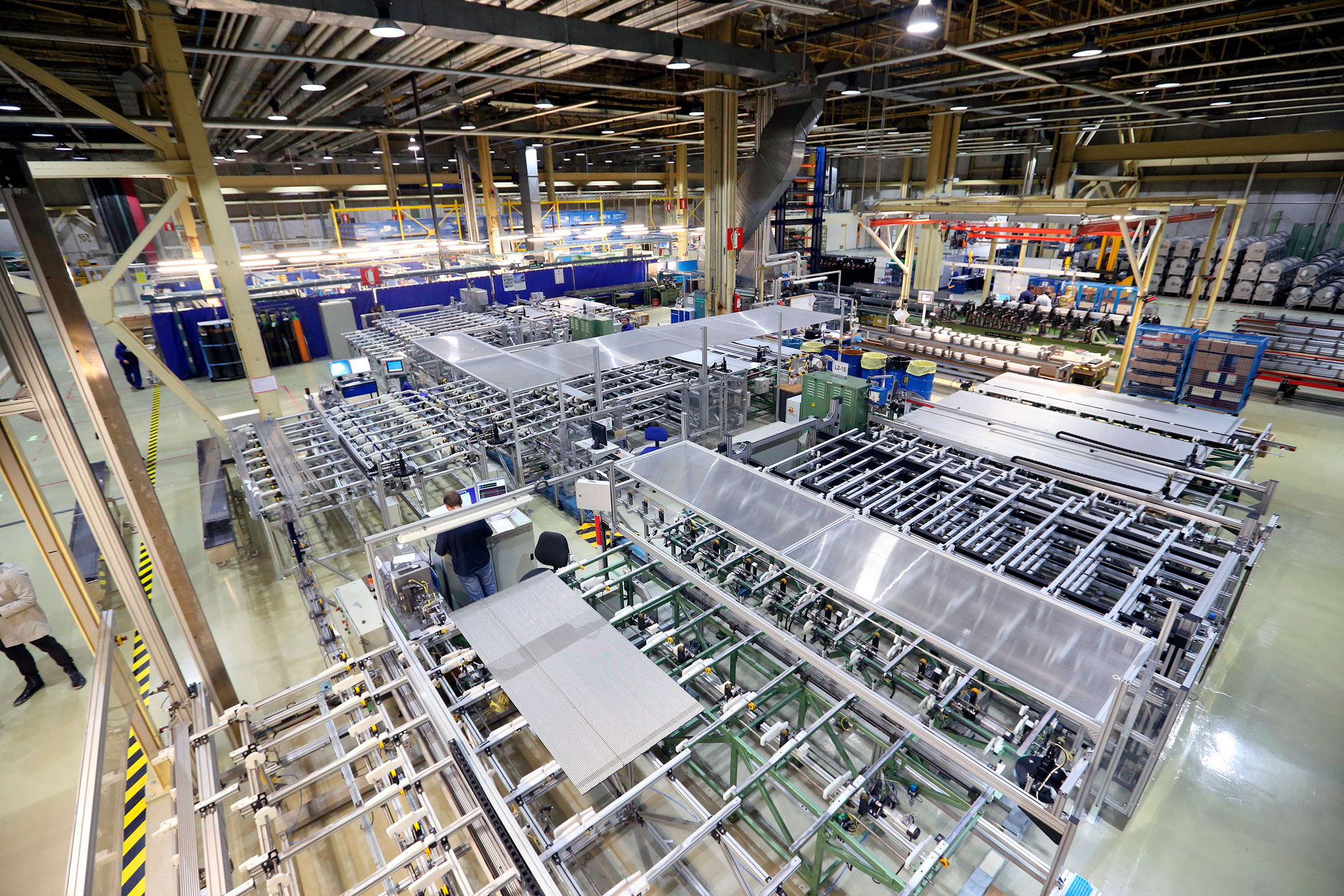
The fuel assemblies are manufactured in our factory in Juzbado (Salamanca).
The activity focuses on the collection of uranium and the components necessary for the process, engineering and the manufacture of fuel assemblies for Spanish and European nuclear power plants, integrating the most innovative technology and the latest advances on the market. These fuels are of three types:
- PWR: Pressurised water reactors, under license from Westinghouse
- BWR: Boiling Water Reactors, General Electric
- VVER: Pressurised water reactors, in collaboration with Westinghouse
The manufacture of fuel assemblies is divided into two processes: ceramic process and mechanical process.
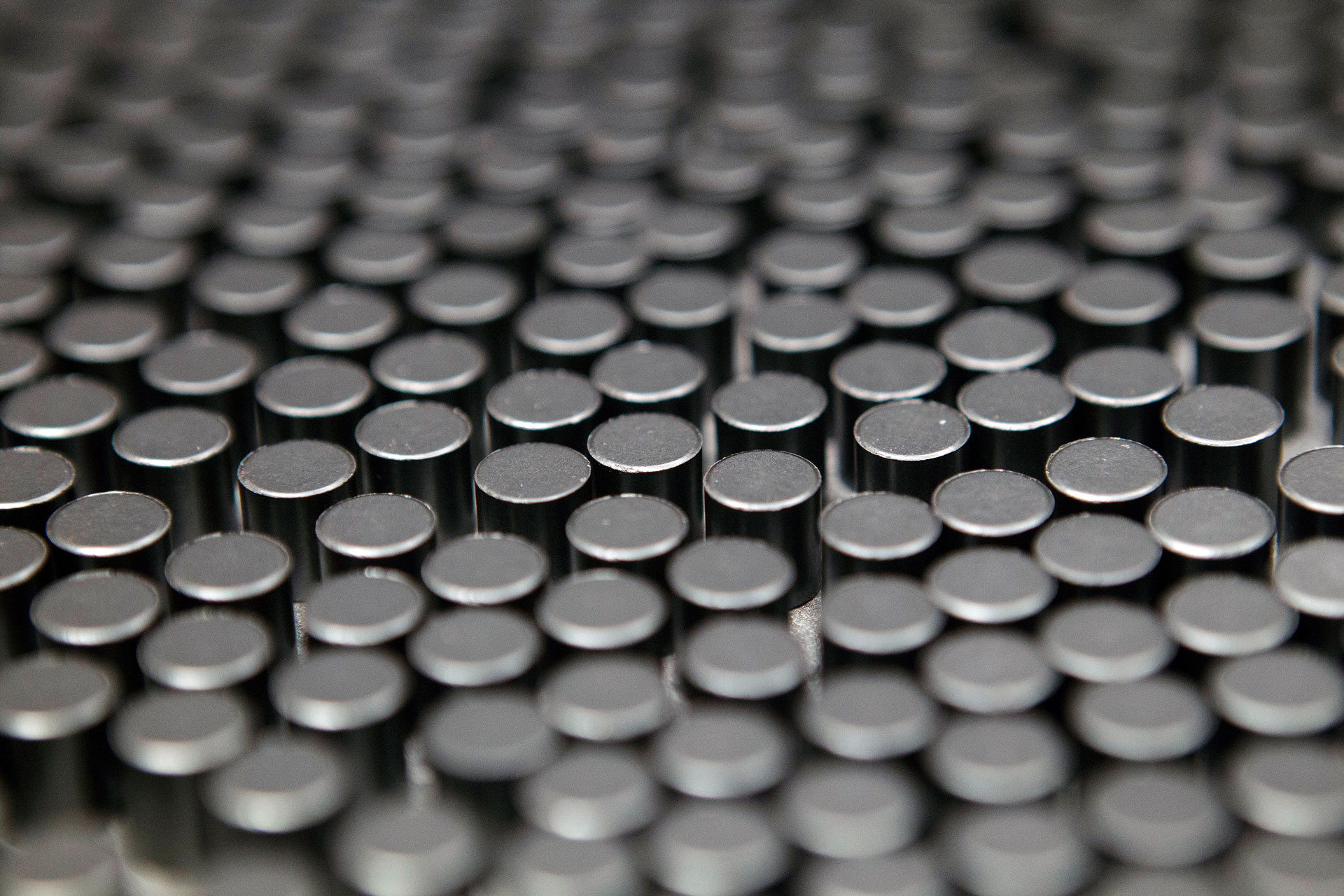
Ceramic process
Uranium oxide powder is made into pellets which are placed in zirconium alloy tubes. Once loaded, pressurised and sealed, they are called fuel rods.The first operation is the reception of drums of uranium oxide powder.
The next step is the mixing which involves the creation of a uniform mixture of virgin uranium oxide powder (UO2) and clean recycled material (U3O8) and usually a pore former.
This is followed by pre-pressing and granulation, which consists of pressing the powder to form a pellet with a higher density which, once sieved, produces a granulated powder that has good flow characteristics.
The granulated powder is pre-mixed with a lubricating powder in a suitable homogeniser, to promote the formation of the pellet during pressing and to guarantee the life of the press.
The pressed pellets undergo a sintering processi.e. to obtain pellets with the appropriate density and integrity for nuclear reactor use. The pellets are sintered at high temperatures resulting in increased strength and hardness of the pellet structure.
The rectification.The nuclear fuel is designed with a specific pellet and cladding diameter. This pellet diameter allows a certain clearance between the inner wall of the cladding and the pellet according to the plane.
Finally, the tablets are measured with laser methods and examined superficially with robotic systems of inspection by artificial vision by means of high-definition cameras. In this way, tablets that do not meet the set quality standards are identified and eliminated.
Uranium oxide recovery by oxidation. The pellets removed at any stage, and especially at the inspection stage, are oxidised and recovered as recycled uranium oxide which is fed back into the mixer.
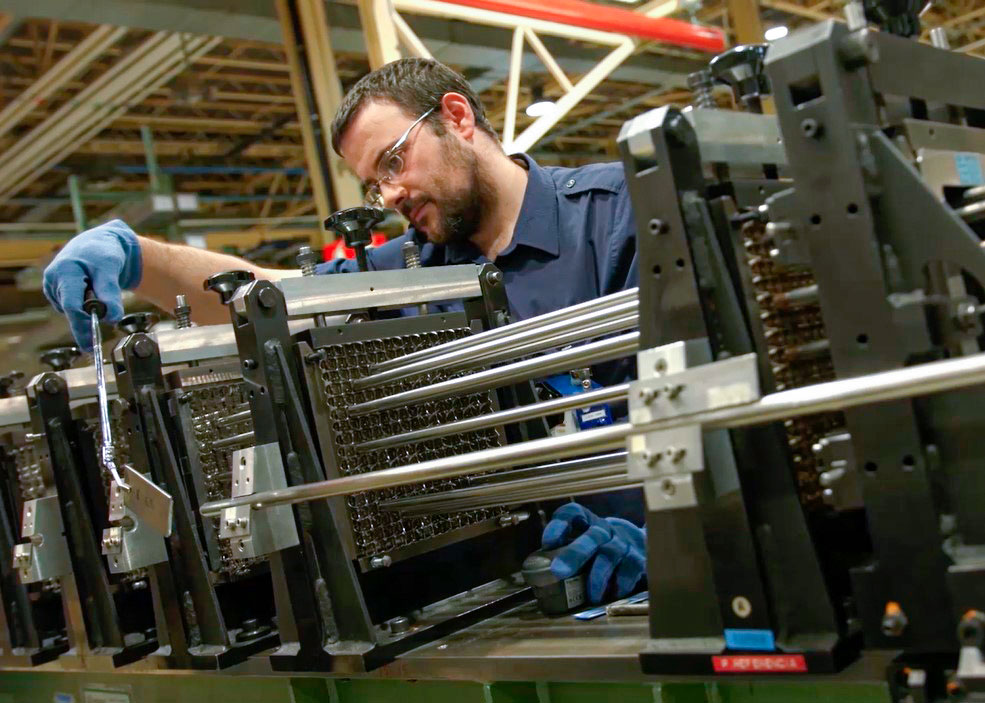
Mechanical process
The fuel rods are assembled into fuel assemblies that are shipped to the power plants.
In this second phase, first plugs are manufactured from zircaloy rods. Once inspected, they are used to seal the fuel rods.
For the production process of fuel rods, tubes to which the bottom cap has been welded at one end are used for loading the rods, i.e. the pins are inserted into the tubes.
Once loaded, the tubes are fitted with a spring inside them, the second plug and, after pressurisation with an inert gas, the second plug is welded on, leaving the finished bar. The rod is subjected to a series of quality controls (ultrasonic, X-ray, He leakage, eddy current and scanners) to verify that it meets all specification requirements.
The next step is the the manufacture of the skeleton,a structure made up of rods, heads and grids, which, after inspection, will serve as a support for inserting the fuel rods.
Final assembly: Due to their different constitution, a difference is made between PWR and BWR fuel assemblies.
Generally speaking, this last operation of the process consists of the insertion of the fuel rods into the skeleton, finally, fitting the heads and support structures.
The fuel assemblies are subjected to various inspections prior to being packed in approved containers for transport. Some designs have a washing stage prior to packaging.
From the beginning, our factory has been committed to a continuous process of technological development of its manufacturing and inspection equipment in collaboration with leading companies.
We develop the necessary equipment and processes in-house to manufacture the different products with the highest safety, quality and efficiency..
The development and optimisation of the inspection and manufacturing equipment we use places ENUSA in a privileged position to supply highly advanced equipment for nuclear fuel factories, a line of business in which we have been working for several years, either individually or in collaboration with other partners such as Tecnatom.
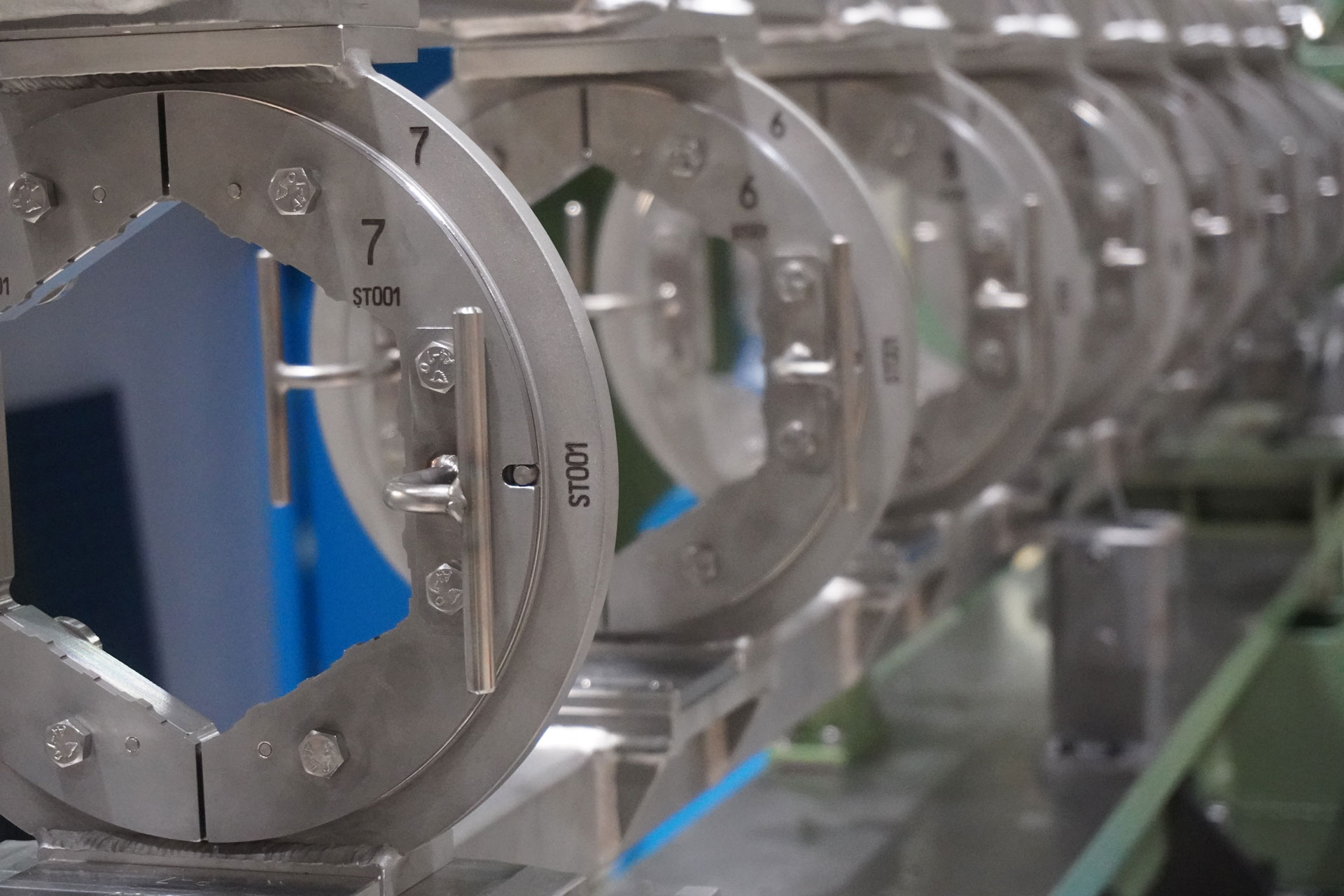
Services in central
We manufacture for Spanish and European nuclear power plants, integrating the most innovative technology and the latest advances on the market.
As a result of ENUSA's concern for the close and direct monitoring of the behaviour of fuel in operation, since the 1980s we have been developing the area of services in central.We coordinate handling, inspection and repair campaigns in line with refuelling programmes, performing fresh fuel reception and irradiated fuel handling services, supervising the process during refuelling outages.
Our performances are:
- Handling of fresh and irradiated fuel.
- Leaking fuel detection by sipping and ultrasonic inspections.
- Visual inspection and control, fuel repair.
- Ultrasonic cleaning.
- Fuel inspection and characterisation.
- Systems for the detection and removal of foreign objects from fuel and other accessible areas.
- Lighting systems and core loading/unloading control.
- Ultrasonic fuel cleaning to remove crude oil deposits from the surface of the rods.
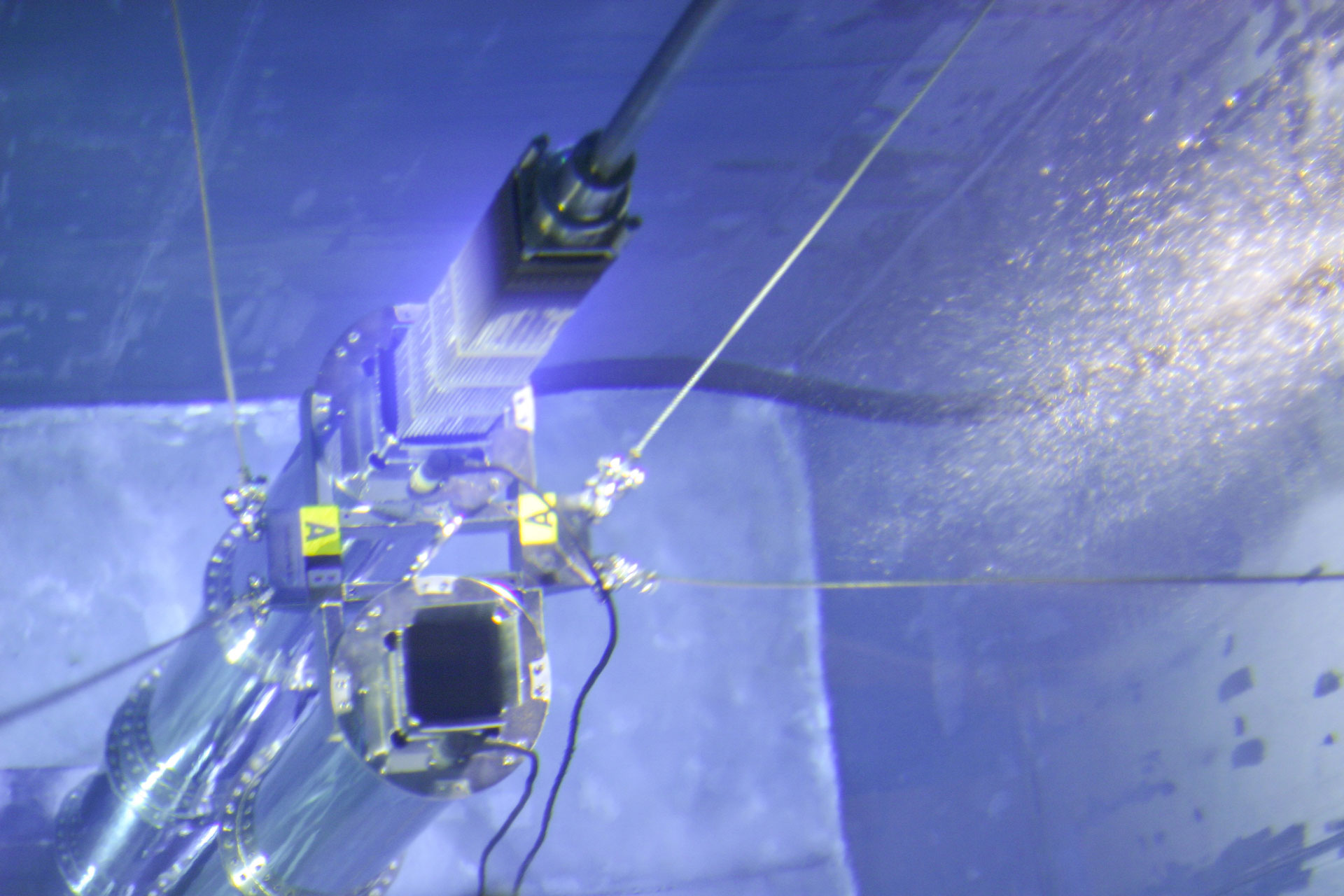
WORKING TOGETHER WITH TECNOCOM
The first services carried out at ENUSA were aimed at checking the behaviour of the fuel by means of inspections and measurements of the most representative characteristics. For this purpose, we developed together with Tecnatom SICOM equipment, which, with updates and innovations, is still in use today in nuclear power plants. The family of SICOM equipment continues to grow to incorporate new capabilities and to meet the most current needs.
90'S
In the 1990s, ENUSA began to provide fuel leak inspection and fuel repair services, and progressively we began to provide the entire portfolio of services described in the preceding paragraphs. In 1995 we founded the subsidiary ENUSA-ENWESA AIE that works with fuel, PWRand in which participate as partners ENWESA Operations and Westinghouse Technology Services (WTS).We have also developed specific services for BWR fuel with GENUSA.The current equipment we have developed in collaboration with our technology partners and other Spanish companies contains advanced technological solutions.
PRESENT
In recent years, we have been carrying out campaigns in practically all the Spanish plants, in European plants where we supply fuel and, occasionally, in other continents, with campaigns in the Angra (Brazil) and Maanshan (Taiwan) plants. In addition, in 2007 we signed an agreement between ENUSA and Tecnatom for the provision of services in China, a market where we have already exported our experience, technology and know-how.
En ENUSA llevamos un seguimiento cercano y directo del comportamiento del combustible en operación.
Provision of irradiated fuel inspection equipment
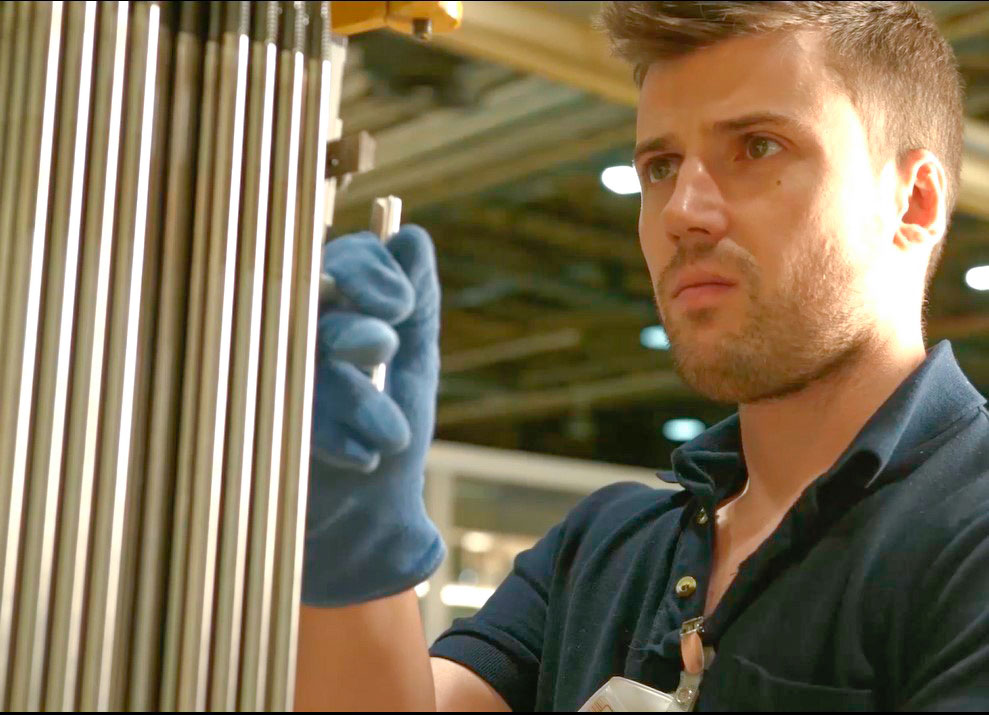
As a result of all this experience, at ENUSA we are also prepared to carry out the necessary activities for the management of irradiated fuel.We are currently involved in different plants, where activities are carried out to inspect, condition and classify fuel assemblies for dry storage. With this commitment, we are also developing the technology and processes necessary to support our customers throughout the fuel cycle.
Based on the experience gained from the provision of services in the plant and the development of our own technology in the inspection of irradiated fuel, we have opened a commercialization channel. We have a wide range of equipment, the most important of which is the family of SICOM equipment, desarrollada juntamente con Tecnatom.
Dismantling and Radioactive Waste Management
We manufacture for Spanish and European nuclear power plants, integrating the most innovative technology and the latest advances on the market.
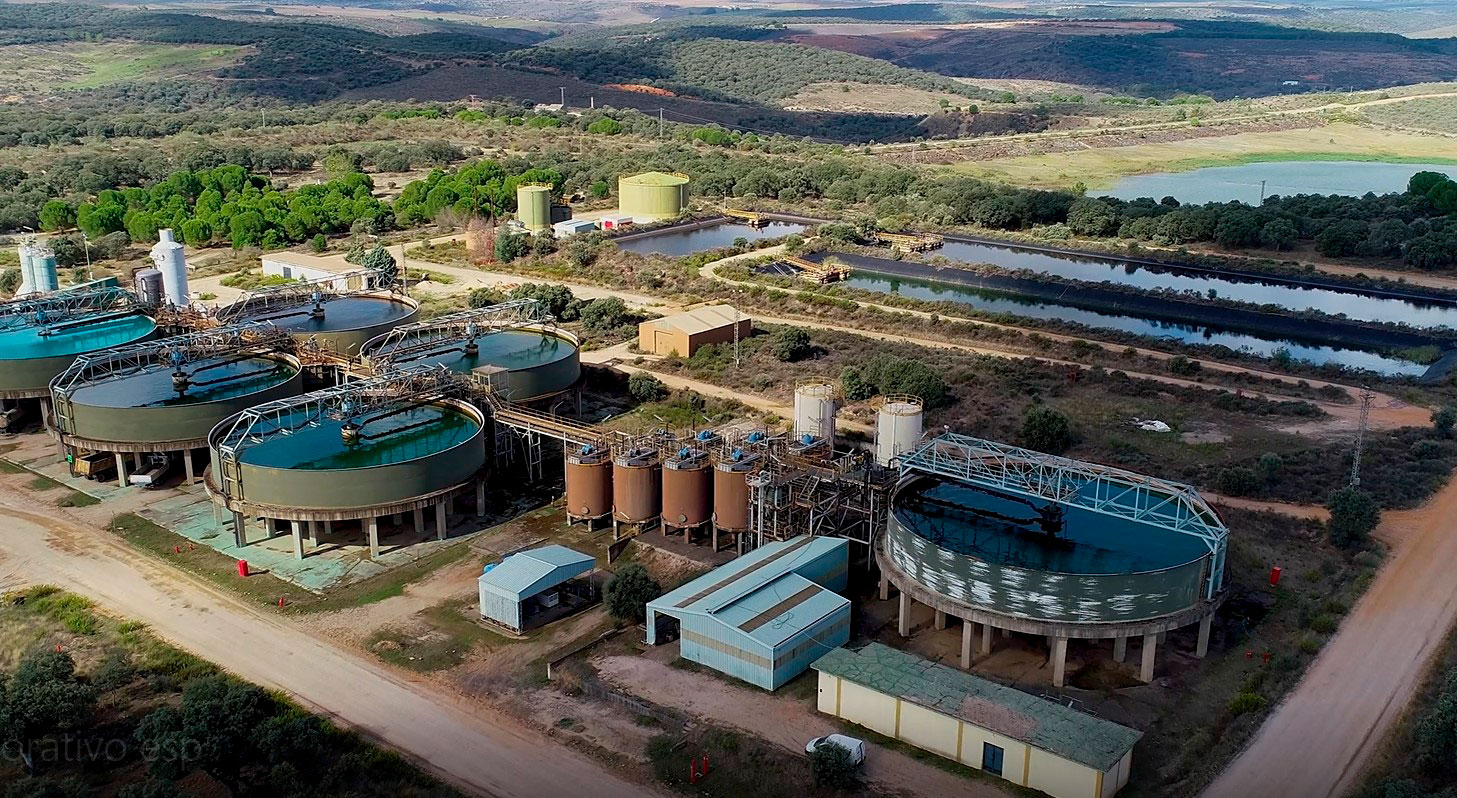
Committed to the environment and sustainable development, at ENUSA we work in the area of nuclear facility decommissioning and radioactive waste management on solutions that allow us to automate radiological characterisation of walls, land and waste, with the consequent reduction of doses for workers, optimisation of execution times and reduction of the volume of waste generated during the dismantling of Nuclear Power Plants.
From an operational point of view, we are aware of the importance of minimising the volume of waste. In this line, we are making a great effort in the technological development of projects, installations and solutions for the decontamination of waste and surfaces, the reduction of the volume occupied by the waste generated, and the reduction of the volume of waste generated and the declassification of materials for their revaluation or storage as conventional waste.
The technological component and innovation, linked to the qualification of personnel and process automation, are a fundamental part of the work we do, which is why ENUSA is building an Equipment Technology and Maintenance Centre as an operations centre for the development of these activities.
- Development of equipment, robotisation of activities and qualification of personnel.
- Radiological characterisation of soils.
- Radiological characterisation and declassification of walls.
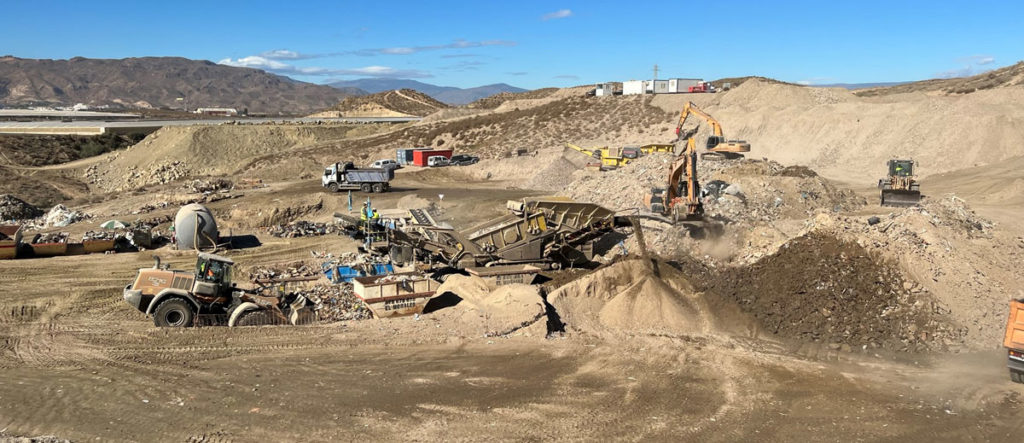
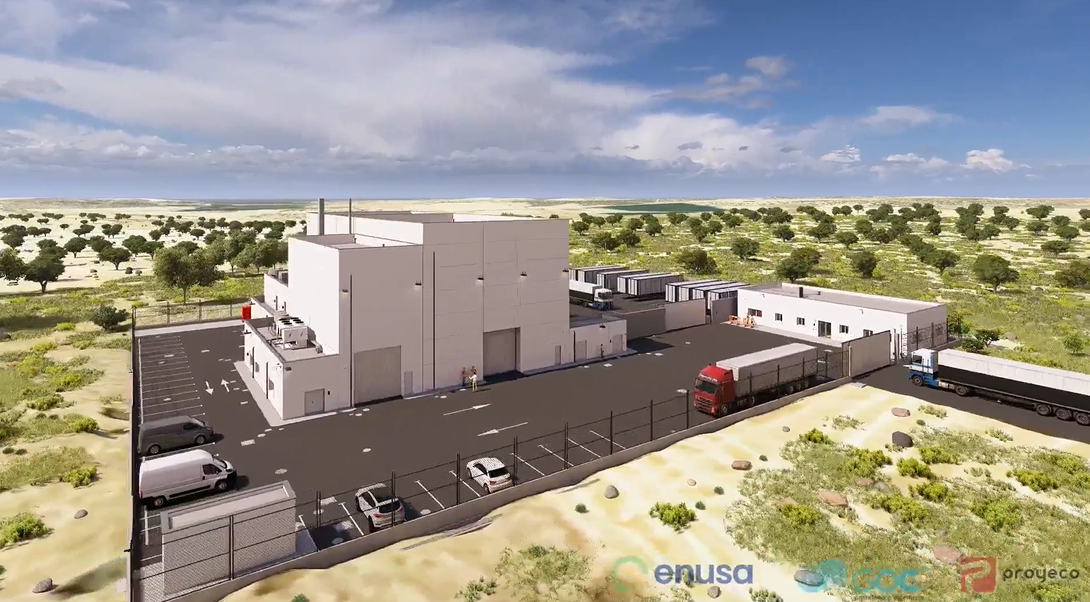
CTME: Centro de Tecnología y Mantenimiento de Equipos
El objetivo de esta nueva construcción es dar solución a la intención de Enusa de realizar la logística, mantenimiento, reparación, calibración y pruebas de los equipos utilizados en las instalaciones de nuestros clientes, además de un Centro Tecnológico donde desarrollar nuestro I+D+i.